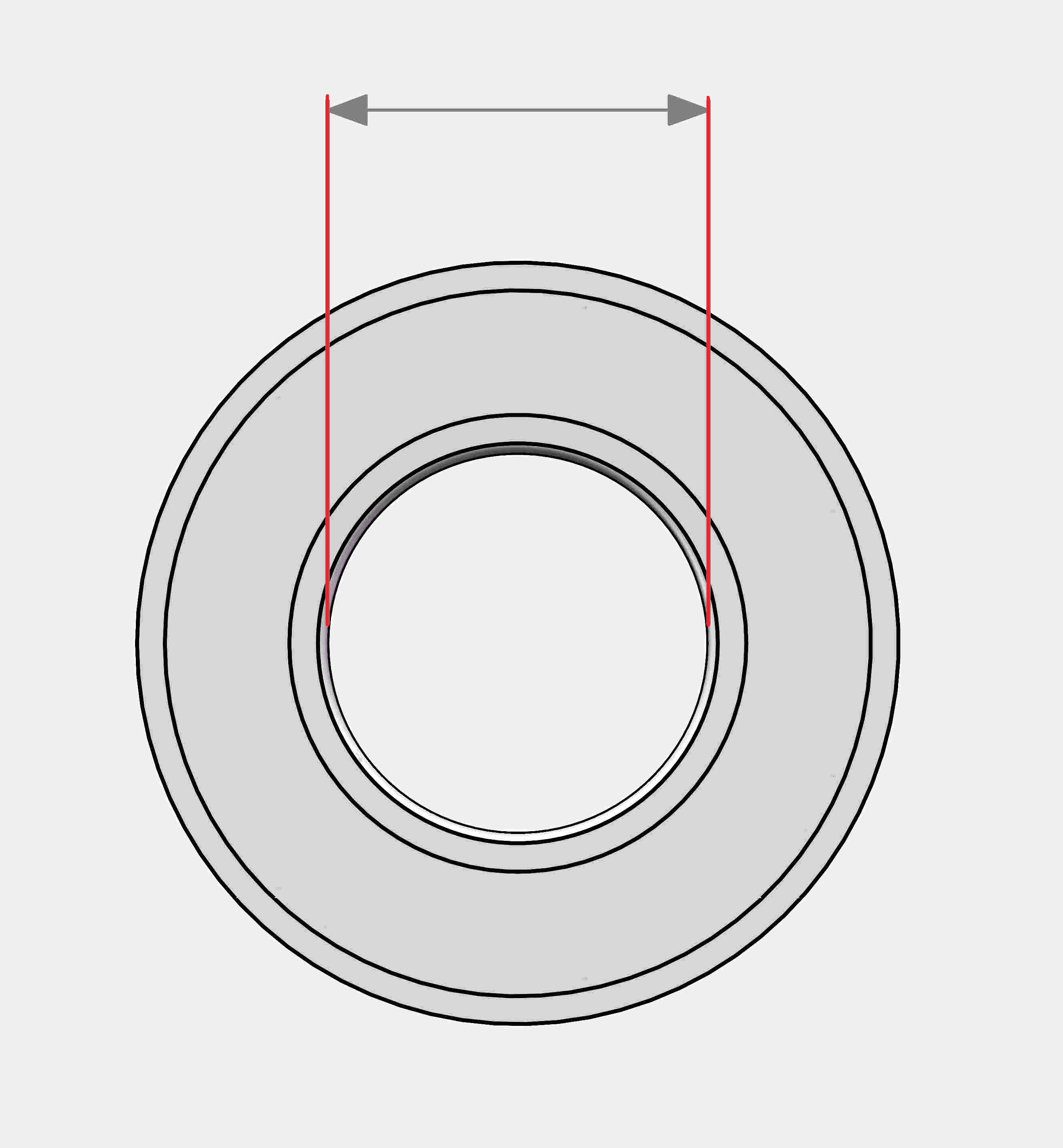
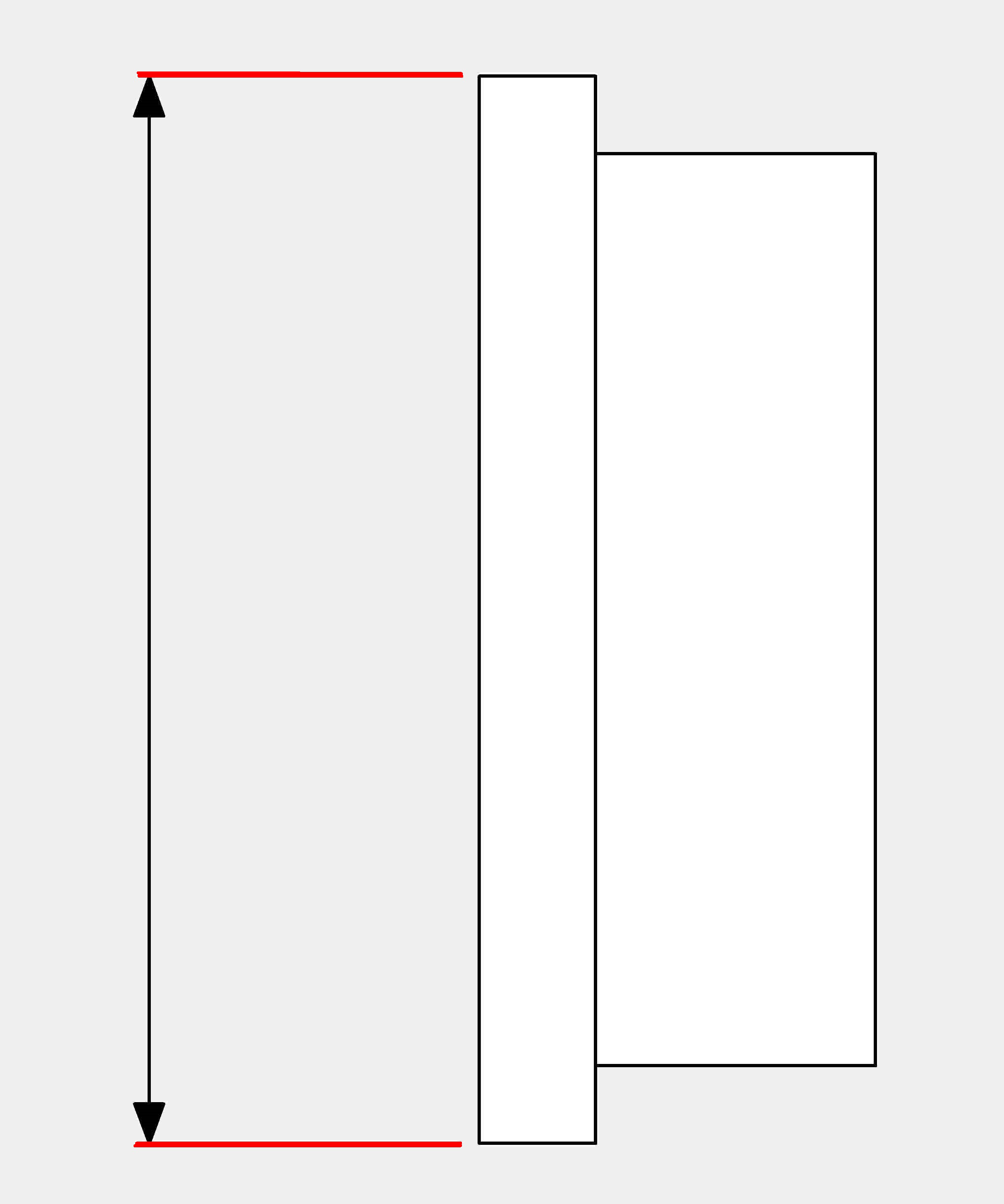
Ball Bearings
17328 ProductsBall bearings are an integral component in many mechanical systems, designed to reduce friction and enable smooth movement between two or more parts.
What are Ball Bearings?
Ball bearings are mechanical components consisting of a set of balls held together in a ring or cage. They're typically made of materials such as steel or ceramic, and a retainer or cage keeps them evenly spaced apart.
How do Ball Bearings Work?
Ball bearings function by rolling instead of sliding, decreasing surface contact and, therefore, the amount of friction. When the balls come in contact with the surfaces of the parts, they roll along them, allowing for smoother movement with less resistance. They can handle radial and axial loads, making them useful for a broad range of applications.
Types of Ball Bearings
Several different types of ball bearings have distinct designs and applications. The most common types of ball bearings are:
◆Deep Groove Ball Bearings: They have a single row of balls arranged in a deep groove, making them capable of handling both radial and axial loads.
◆Angular Contact Ball Bearings: These bearings can handle axial loads in one direction and have two rows of balls angled with respect to each other.
◆Thrust Ball Bearings: They're designed to handle axial loads in both directions, with a single row of balls arranged in a circular raceway.
◆Self-Aligning Ball Bearings: These bearings compensate for misalignment between the shaft and housing, with two rows of balls arranged at an angle.
Applications of Ball Bearings
Ball bearings have a wide range of applications, from household appliances to heavy machinery. Some common applications of ball bearings are:
◆Automobiles: They're used in the wheels, transmission, and engine to reduce friction and improve performance.
◆Aerospace: They're used in aircraft engines, landing gear, and control systems to reduce weight and improve efficiency.
◆Industrial Machinery: They're used in pumps, motors, and conveyor systems.
◆Household Appliances: Ball bearings are used in washing machines, dryers, and refrigerators to improve performance.
In conclusion, ball bearings are essential in many mechanical systems. They function by reducing friction and enabling smoother movement. With the ability to handle both radial and axial loads, ball bearings are suitable for a broad range of applications, from household appliances to heavy machinery.