Polyurethane Rollers: Advantages & Uses
In the modern industrial world, polyurethane rollers are key players. They help many processes run smoothly and efficiently, proving to be both robust and adaptable in a range of applications. In this blog, we will explore the unique features and benefits of polyurethane rollers, as well as their wide use in different sectors. Join us as we delve into the important role these rollers play in the industry.
What is a Polyurethane Roller?
Polyurethane rollers, made from polyurethane elastomer, bridge the gap between rubber and plastic. This elastomer is produced using isocyanates, including PPDI, MDI, TDI, and NDI. While these ensure robust thermal performance, NDI-based products might show a taupe color due to yellowing on light exposure.
Polyurethane, an engineering marvel, boasts of attributes suitable for roller applications. Key properties include:
- Flexibility: It is the ability of polyurethane to withstand tensile forces that tear the material apart and tear its bulk. Polyester-type polyurethane has the highest tear strength. Polyurethane has a tear strength of up to 1000 pounds per linear inch according to ASTM D-624 Type C testing.
- Wear resistance: Polyurethanes are highly resistant to sliding and impact. Due to its low friction coefficient and high strength, it is not affected by sliding wear. Through impact wear, it absorbs the energy of particle attack, disperses stress, and recovers instantly without any sign of damage. Polyurethane is blended to have properties such as a low coefficient of friction, high tear strength and elasticity, which help it withstand wear and tear. Its resin composition gives it excellent wear resistance. Among the polyol compounds used to make polyurethane, polyester has the best tear and abrasion resistance.
- Chemical Stability: The chemical resistance of polyurethane depends on the type of polyol used in its polymer system. Ether-based systems are more resistant to water, making them suitable for wet applications. Ester groups, on the other hand, are most resistant to oils, solvents, and most petroleum compounds.
Types of Polyurethane Rollers
Polyurethane Rollers with Bearings
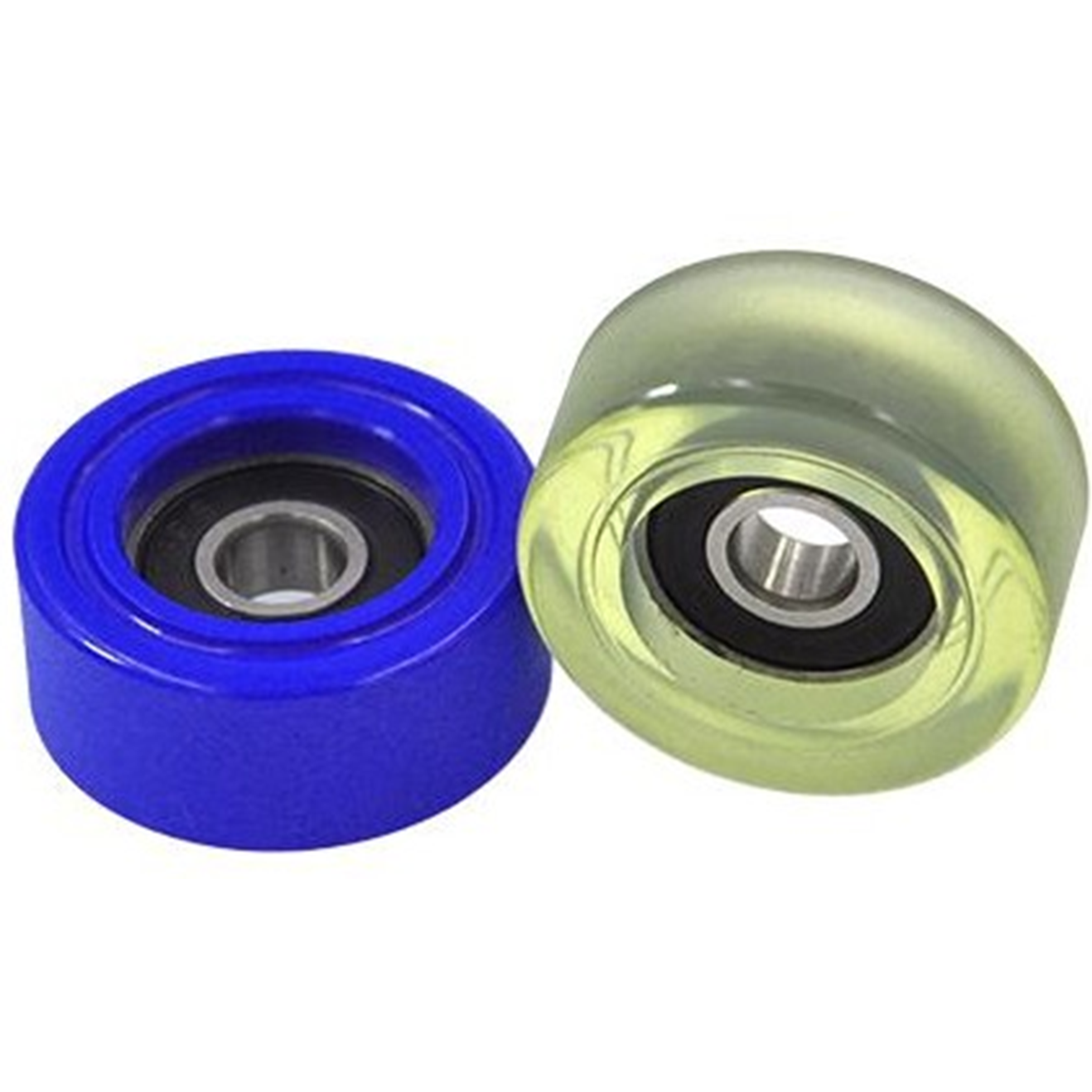
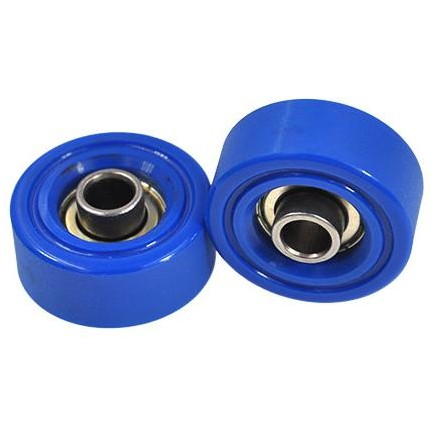
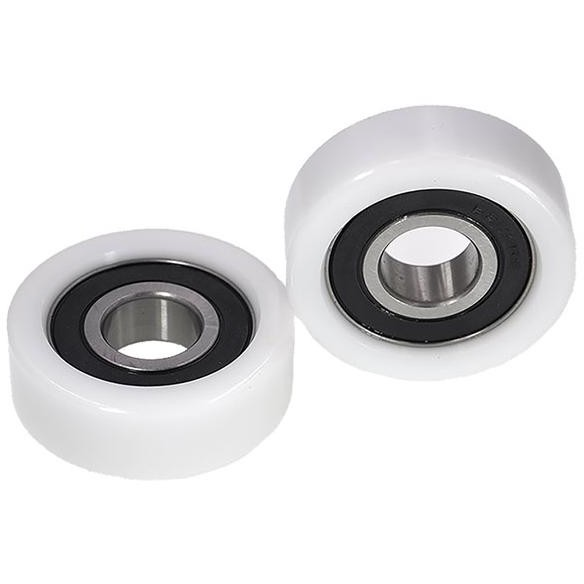
Polyurethane Rollers with Screw
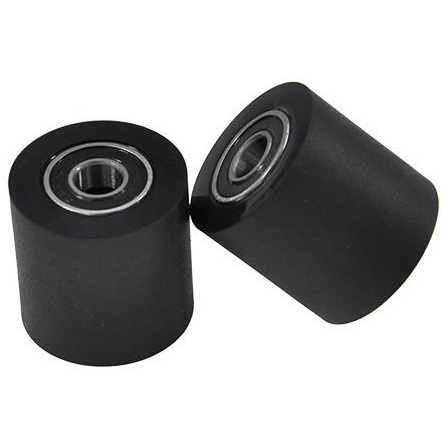
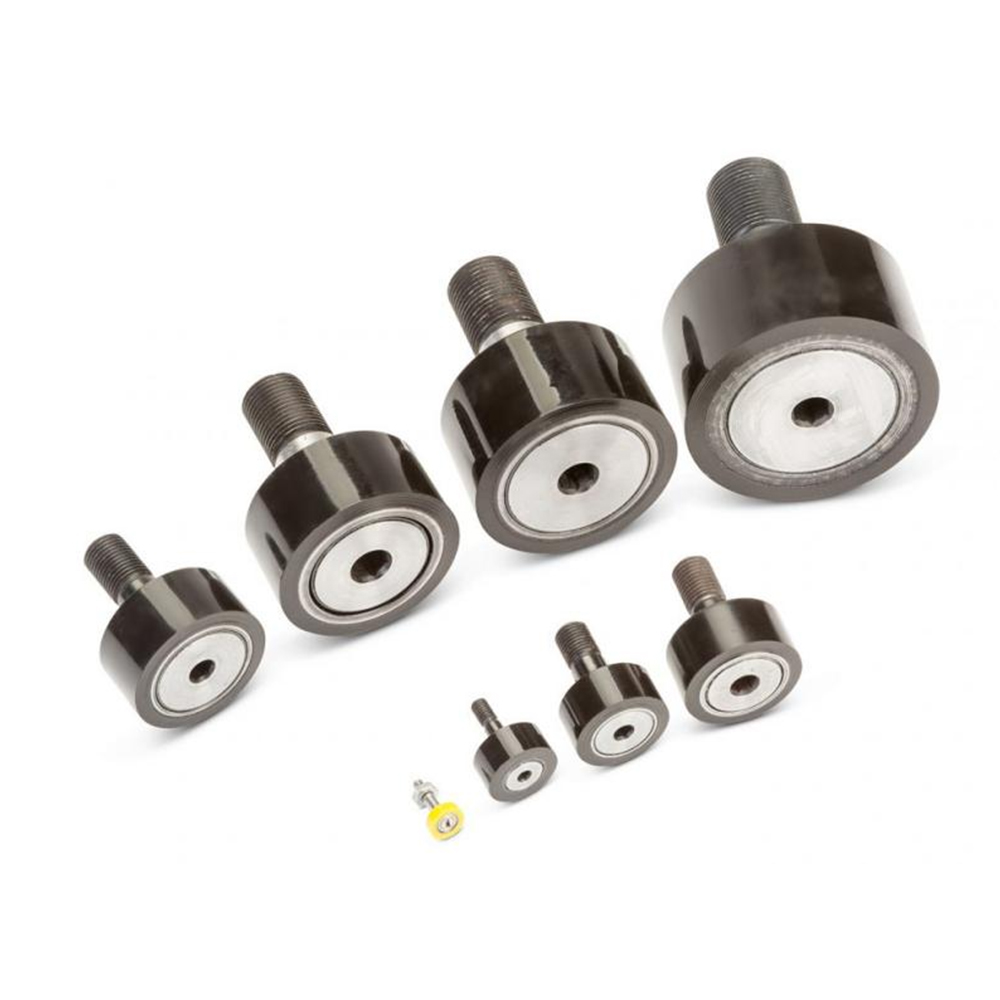
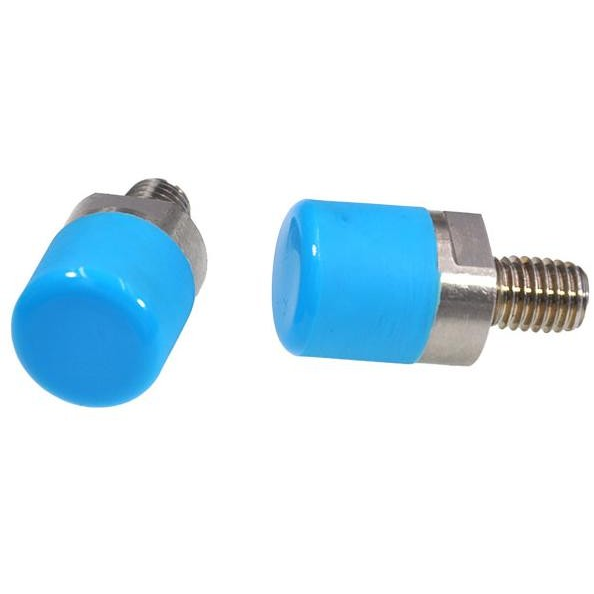
We also provide Outsourcing Polyurethane bearings and Outsourcing POM bearings.
Advantages of Polyurethane Rollers
Superior Durability
The durability of Polyurethane Rollers is evident in these key areas:
- Lifespan: Polyurethane rollers last 4,000 hours, outliving rubber's 1,000 hours.
- Mechanical Strength: Resistant to tears and crushing, ensuring a longer service life.
- Chemical Resistance: Effective against oils, solvents, and some acids/bases, suitable for varied industries.
- Heat Tolerance: Works up to 80°C and withstands brief peaks of 120°C.
- Environmental Adaptability: Polyurethane rollers can resist UV, ozone, and grease, ideal for both indoor and outdoor uses.
Robust Load Support of Polyurethane Rollers
Polyurethane rollers excel in supporting heavy loads. Their strength comes from:
- Molecular Structure: Polyurethane is built from strong chains that give it both power and flexibility, letting rollers bear weight without deforming.
- Adjustable Firmness: Manufacturers can tweak polyurethane's hardness to suit different needs, from soft to very firm. In detail, hardness of Polyurethane Rollers ranges from 10A to 75D durometer.
- Natural Stretch: Polyurethane is elastic. It can endure heavy weights and still bounce back to its original shape.
- Solid Connection: It binds especially well to metals, ensuring the roller's weight is spread evenly and lasts longer without issues.
- Excellent Grip: Polyurethane rollers offer superior grip on materials, including challenging ones like glass or frosted wood. Their enhanced grip and adaptability make them more efficient than rubber or plastic counterparts, leading to their widespread use in various industries.
Enhanced Productivity
Polyurethane rollers offer enhanced durability, minimizing replacements and reducing maintenance downtime, thereby boosting productivity.
Safety, Compliance & Hygiene
Meeting FDA Standards for Food Processing
Polyurethane rollers are FDA-approved for food processing, ensuring food safety. They're a better choice than rubber or plastic options.
Residue and Mark-Free Performance
Rubber roller linings add carbon black as filler and reinforcement. When rolled on hard surfaces with enough force, they can leave dark streaks and marks that can cause damage in applications such as finished product handling and printing. Polyurethane rollers, on the other hand, do not require a carbon roller liner for additional support, which avoids the possibility of carbon black.
Cost-Effectiveness
Polyurethane is easier and cheaper to manufacture than most other materials and can reduce downtime and the need for repairs and replacements due to its high wear resistance and long service life.
Delving into Polyurethane Roller Applications
Applications of Polyurethane Rollers Across Industries, such as:
- Manufacturing: Polyurethane rollers streamline assembly lines and automation, enhancing operational efficiency and roller longevity.
- Automotive: Integrated into vehicle assembly and component handling, these rollers boost production velocity and exactitude.
- Mining: Essential in conveyor systems and material handling, they bolster both safety and productivity metrics.
- Food Processing: Emphasizing hygiene and FDA standards, Polyurethane rollers are indispensable in both processing and packaging stages.
- Aviation: Employed in aircraft manufacturing and upkeep, their presence ensures precision and dependability.
- Packaging: These rollers facilitate handling of diverse products and bolster efficiency in swift packaging processes.
- Printing: Crucial in print machinery, polyurethane rollers ensure color accuracy and endure high-pressure operations.
- Agriculture: Found in modern farming tools and irrigation systems, they support cutting-edge agricultural practices.
- Banking: Integral in document processing and ATMs, enhancing both security measures and operational efficiency.
- Construction: Utilized in material management and machinery operations, they aid in fortified construction methodologies.
- Steel Cutting: Applied for meticulous cutting and material management, their abrasion resistance prolongs operational lifespan.
Choosing the Right Polyurethane Roller
Looking for the right polyurethane roller? Keep these simple tips in mind:
- Understand Your Needs: Think about load, speed, and the environment it'll work in.
- Check for Standards: If it's for food use, it should meet FDA guidelines.
- Choose a Trusted Brand: Quality and durability matter.
- Think Custom: Some urethane rollers can be tailored just for you.
With these points, finding your perfect polyurethane roller becomes easy and straightforward.
Keep Learning