Cancel
MR624C THB/C3 AF2
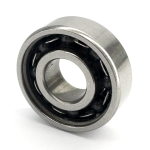
Price $ 8.68
Number
Part Number | MR624C THB/C3 AF2 |
System of Measurement | Metric |
Bearing Type | Ball |
For Load Direction | Radial |
Construction | Single Row |
Inner Ring Type | Standard |
Seal Type | Open |
Bore Dia | 4 mm |
Outer Dia | 13 mm |
Width | 5 mm |
Ring Material | Chrome Steel |
Balls Material | Si3n4 |
Cage Material | Phenolic |
Lubrication | Shell Af2 Oil |
Shaft Mount Type | Press Fit |
Temperature Range | -86 to 230 °F |
ABEC Rating | Abec#1/isop0 |
Radial Clearance Trade No | MC3 |
Ball Grade | 5 |
RoHS | Compliant |
REACH | Compliant |
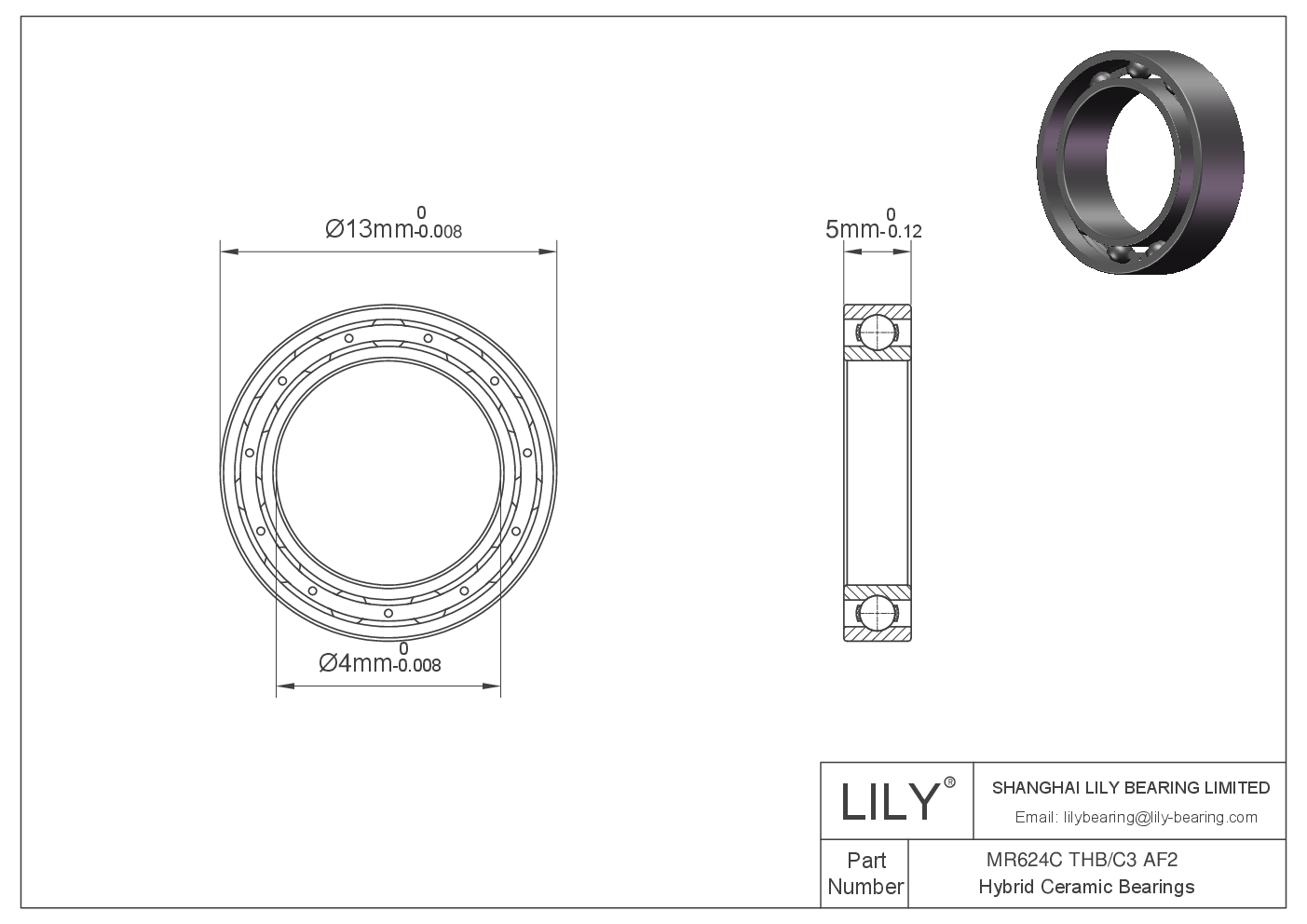
Design Features of MR624C THB/C3 AF2 Bearing
MR624C THB/C3 AF2 Bearing utilizes ceramic balls, typically made of silicon nitride (Si3N4), combined with steel inner and outer races. MR624C THB/C3 AF2 bore dia is 4 mm. Its out dia is 13 mm. MR624C THB/C3 AF2 width is 5 mm. This Bearing provides a sophisticated, high-performance solution that caters to the unique challenges presented by modern industrial and technological applications.
What Benefits Can MR624C THB/C3 AF2 Bearing Provide?
- Reduced Friction: Ceramic's low frictional properties ensure smoother operation and decreased heat generation.
- Enhanced Durability: The wear-resistant nature of ceramic extends the bearing's lifespan, particularly in demanding conditions.
- Corrosion Resistance: Ceramic balls resist moisture and chemicals, safeguarding the bearing from corrosive environments.
- Electrical Insulation: Its non-conductive composition prevents electrical arcing, essential in electrically active setups.
- High-Speed Operation: Its attributes permit this bearing to operate efficiently at elevated rotational speeds.
What Can MR624C THB/C3 AF2 Bearing Be Used for?
MR624C THB/C3 AF2 Bearing is employed in various applications due to its unique characteristics. It can be used for:
- Electric Motors: Ideal for preventing electrical arcing, especially in electric vehicles.
- Precision Machinery: Suited for high rotational accuracy needs.
- Aerospace: Meeting the demands of wear resistance and thermal stability.
- High-Frequency Machining: Beneficial for high-speed spindles and machining centers.
- Harsh Environments: Resisting corrosion and withstanding extreme temperatures.
Recommended Products